Final Program for the 11th JFPS International Symposium on Fluid Power, HAKODATE 2020
The research papers and presentation videos are available for those who registered to the symposium from October 12 until October 31, 2021, through the Final Program.
Regarding the online streaming sessions, login information to Zoom webinar is announced to those who registered to the symposium by e-mail.
Invited Lecture
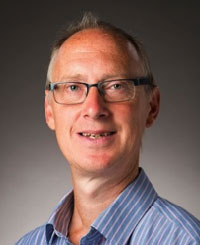
"Piezoelectric pumps for hydraulic actuation"
Prof. Andrew Plummer, University of Bath
Professor Andrew Plummer received his Ph.D from the University of Bath in 1991, for research into control of electro-hydraulic systems. He worked as a research engineer for Thales from 1990, developing flight simulator control technology, before joining the University of Leeds in 1994. From 1999 until 2006 he was global control systems R&D manager for Instron, manufacturers of materials and structural testing systems. He is now Director of the Centre for Power Transmission and Motion Control, University of Bath, and has published 180 papers in the field of motion and force control, many relating to electro-hydraulic servo-systems. Prof. Plummer is Past Chair of the Institution of Mechanical Engineers Mechatronics Informatics and Control Group and also the UK Automatic Control Council, and is Associate Editor of both the International Journal of Fluid Power and Control Engineering Practice. He is Chair of the Global Fluid Power Society.
Abstract: There is an increasing demand for small-scale hydraulic actuation systems, working at around the one hundred watts range, for example in human-scale robot applications. Pump-controlled actuators, where motion is controlled by varying the flow delivered to an actuator by a dedicated pump, are potentially energy efficient and allow the well-known flexibility in system design and control provided by hydraulics. However, compact and effective variable-displacement or variable-speed pumps for delivering in the region of 1 L/min and 100 bar are not widely available. Piezoelectric pumps are a possible solution. A single-cylinder piezoelectric pump consists of a piezoceramic actuator – either a stack or a bending actuator – vibrating a piston in a pumping chamber connected to suction and discharge lines by valves which rectify flow. Piezopumps have been found to be commercially viable in some low power fluid movement applications (10mW order of magnitude), for example in medicine. However, higher power piezopumps are still a matter of research. In this presentation I describe developments in this field, including reviewing some previous and current research, and describing the technical challenges and possible solutions.
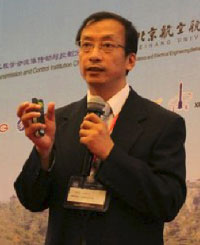
"Research on high performance electro-hydrostatic actuator (EHA) system"
Prof. Zongxia Jiao, Beihang University
Prof. Zongxia Jiao is from Beihang University, Beijing, China. He is currently director of the Fluid Transmission and Control Branch of the China Mechanical Engineering Society, honorary Director of the Electromechanical Branch of the China Aviation Society, Changjiang distinguished professor, winner of the National Science Fund for Distinguished Young Scholars. He has been engaged in the theory, key technology and equipment research of electro-hydraulic servo systems and basic components. He has also worked in the field of the reliability and high-performance control of the aircraft hydraulic system, the key technology and equipment of high-efficiency braking system, high-reliability hydraulic system and electro-hydraulic servo control. Prof. Jiao has been granted 2 National Technology Invention Awards (2nd class) and 1 National S&T Progress Awards (2nd class) and has established the IEEE/CSAA Aviation Electromechanical Series International Conference. He has published more than 300 papers including 6 ESI high cited papers.
Abstract: More/All-electric aircraft are currently the development trend of aircraft. Electro-hydrostatic actuator (EHA) is a highly integrated actuation in power-by-wire aircraft utility system, including an electrical motor, pump and cylinder. EHA has the advantages of easy maintenance and good controllability. But its dynamic behavior is relatively low and the temperature increment is fast, which restrict the use of EHA. In order to overcome these disadvantages, a new design of EHA which features active load-sensitive has been developed. Active load-sensitive is achieved by using a special pressure control valve to actively control the variable pump. It adjusts the displacement of pump according to load pressure feedback and position feedback intelligently, which keeps the advantage of high efficiency but also overcomes the weakness of low rigidity. Especially in the high load condition, the temperature of the motor can be reduced significantly. Both simulation and experiment results indicate the performance improvement of the EHA.
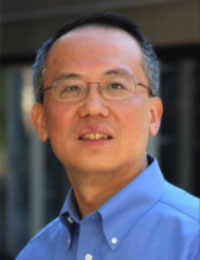
"Fluid Power: from Motion Control to Powertrain Innovation"
Prof. Zongxuan Sun, University of Minnesota
Zongxuan Sun is a Professor at the Department of Mechanical Engineering, University of Minnesota. He received his Ph.D. degree in Mechanical Engineering from University of Illinois at Urbana-Champaign in 2000. He is currently Director of the Engineering Research Center for Compact and Efficient Fluid Power (CCEFP). He was a Staff Researcher (2006-2007) and a Senior Researcher (2000-2006) at General Motors Research and Development Center in Warren, MI. His research interests include controls, fluid power, and mechatronics with applications to automotive and commercial vehicle propulsion systems. Dr. Sun has published over one hundred fifty referred technical papers and received twenty two US patents. Dr. Sun is a recipient of the Charles E. Bowers Faculty Teaching Award, George W. Taylor Career Development Award from College of Science and Engineering, University of Minnesota, NSF CAREER Award, SAE Ralph R. Teetor Educational Award, Best Paper Award from ASME Automotive and Transportation Systems Technical Committee in 2018, Best Paper Award from 2012 International Conference on Advanced Vehicle Technologies and Integration, Inventor Milestone Award, Spark Plug Award, and Charles L. McCuen Special Achievement Award from GM R&D.
Abstract: Fluid power is widely used in off-road vehicles including construction machinery and agriculture equipment for driving and working functions. Given the increasing global focus on energy efficiency and environmental impact, powertrain innovation for off-road vehicles is needed. Inspired by this urgent need, we would like to refocus on the fundamental strengths of fluid power and connect them to the energy conversion, power transfer and motion control. This talk will present the study of motion control using fluid power, including accuracy, efficiency, and control bandwidth. Based on the motion control, we will discuss the powertrain innovation using fluid power. Examples will be provided including free piston engine, camless engine, controlled-trajectory rapid compression and expansion machine.
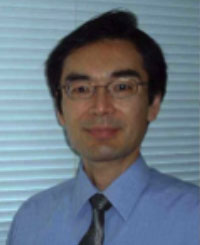
"Tribology Research on Fluid Power in Japan⎯Review and State of the Art"
Prof. Toshiharu Kazama, Muroran Institute of Technology
Toshiharu Kazama is a Professor of the Muroran Institute of Technology since 2006. He joined the Institute as an Associate Professor in the department of mechanical engineering in 1994. Prior to coming to the Muroran Institute of Technology, he has done research work as a Research Associate at Yokohama National University, Japan. Dr. Kazama received his BEng, MEng, and PhD degrees from Yokohama National University. Primary areas of research have been tribology and cavitation as related to fluid power systems and components as well as machine elements and design. He has worked in the fields of internal flow of hydraulic pumps and motors, lubrication of hydrodynamic and hydrostatic bearings, sealing of packing and gaskets, and cavitation of liquid jets and erosion.
Abstract: Hydraulic pumps, motors, and cylinders are the major components in hydraulic systems, which achieve transformation between mechanical energy and fluid pressure. The reliability, efficiency, and performance of such a system depend on the tribology at the interface between its sliding, bearing, and sealing parts. This talk briefly describes the short history of research on equipment tribology in Japan and surveys the knowledge and insights obtained in the last couple of decades, including the activities of research committees in Japan Fluid Power Systems Society (JFPS), and Japan Hydraulic and Pneumatic Society (forerunner of JFPS). With the literature review alongside the cutting-edge technology, theoretical and experimental approaches for these systems in Japan are surveyed. Additionally, our results and efforts mainly regarding pump tests and slipper models in terms of thermal effects, including liquid physical properties, thermohydrodynamic lubrication, and elastic deformation, are presented. Results on roughness effects, including mixed lubrication and surface interaction, are also presented. Finally, challenges in fluid power tribology, future development agenda, and vision, with remarks on scope and perspective, are discussed.