Invited Lecture (Room A) : Oct. 25 (Wed.), 2017
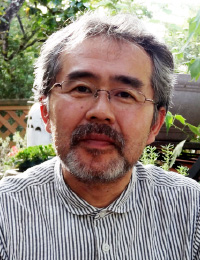
"Fluid Power Pioneering New Robotics"
Prof. Koichi SUZUMORI, Japan
Koichi Suzumori received the B.S., M.S., and Ph.D. degrees in mechanical engineering from Yokohama National University, Japan, in 1982, 1984, and 1990, respectively. He had worked for Toshiba R&D Center from 1984 to 2001, and worked for Micro-Machine Center, Tokyo, from 1999 to 2001. He had been a professor in Division of Industrial Innovation Sciences, Okayama University, Japan from 2001 to 2014. Since 2014 till present, he has been a professor in Department of Mechanical Engineering, Tokyo Institute of Technology. He is mainly engaging in the research fields of new actuators and their applications. He is a fellow member of the Japan Society of Mechanical Engineers and of the Robotics Society of Japan.
Abstract: Robotics started with fluid actuators in year 1960’s where most of the robotic systems apply hydraulic actuators including the first industrial robots, Unimate and Versatran from USA in year 1962. The first humanoid robot developed by Waseda University in the year 1970 was also driven by hydraulic actuators. Apparently, the first wearable robot was developed and driven by pneumatic McKibben muscles in year 1960. From there, development of robots using hydraulic and pneumatic were expanding significantly until 1980’s where high performance electrical motors were introduced. Consequently, since then, the fluid power actuators are categorized as conventional actuators and seldom used in robotics today.
However, fluid powered actuators are NOT too old to be used in current robots because it has a great potential for pioneering a new world of robotics. I will talk about it and show the following examples of fluid actuators and their applications in new concept of robotics. One of them is the "Pneumatic thin artificial muscle" which opens a new area of Musculoskeletal robotics, Giacometti robotics, Soft robotics mechanism, and Power-assist wears. Our "Next-generation hydraulic actuator” with advantage of lightness, compactness, and fine controllability is possible for tough robotics to work in hazard conditions, rescue robotics, and soft high power robotics. I want to share these great potentials of the new fluid power systems in robotics with all participants.
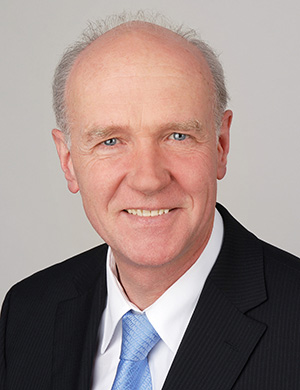
"Some Recent Fluid Power Research Results at IFAS"
Prof. Hubertus MURRENHOFF, Germany
Director, IFAS of RWTH Aachen University
Having studied Mechanical Engineering focusing on fluid power from 1973 on and finishing his PhD in 1983 he started his career as Chief Engineer at the Institute for Hydraulics and Pneumatics at RWTH being in charge of Finance, Engineering and Personnel.
In 1986 he started an industrial career with overseas experience in the aviation business at HSC Controls Inc., Amherst, NY being in charge of Engineering and Marketing as Vice President. Following he took the position of Technical Director of MSM in Memmingen, Germany belonging to the Board as Executive Vice President.
With 8 years industrial experience he joined RWTH again in 1994 and became Executive Director of the Institute for Fluid Power Drives and Controls (IFAS). The institute focuses on all aspects of fluid power and is divided into five research groups covering hydraulics and pneumatics. He was Head of the Collaborative Research Centre “Environmentally Friendly Tribological Systems” over the 12 year funding period and takes now part in the Excellence Cluster “Tailor Made Fuels from Biomass” (TMFB) where IFAS is responsible for the tribological research subjects since 2007.
Abstract: Fluid Power is a drive technology that advanced significantly over the last decades. With its huge power density and the linear drives by simple and robust hydraulic cylinders it can successfully compete with electric and electro-mechanic solutions. However, it faces challenges when it comes to environmental and efficiency issues. With the functional gaps in typical components like displacement units and valves we face leakage and friction as we have a double use of it, namely sealing and easy motion of bodies against each other.
On the one hand this requires tribological and environmental research for the components but we also need to look at the systems on the other side. In the latter we learned that a holistic approach is necessary including the combustion engine into the efficiency optimization of a fluid power drive solution. Thus the talk will focus on results with regard to components for efficiency, noise and performance but will also show the additional value that can be harvested when a consequent use of pressure impressed systems with accumulators for energy recuperation is used over the machine cycles. This requires the consequent use of digital hydraulics as well as independent metering for smart solutions.
Special Lecture 1 (Room A) : Oct. 26 (Thu.), 2017
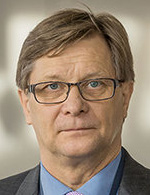
"Sliding autonomy working machines in future worksite"
Prof. Kalevi HUHTALA, Finland
Professor, Tampere University of technology
Professor Kalevi Huhtala is currently Head of Laboratory of Automation and Hydraulic engineering in Tampere University of technology. Laboratory has eight professors and total staff of 100.
He is graduated from Tampere University of technology in 1996. Title of his doctor thesis is “Modelling of Hydrostatic Transmission - Steady-State, Linear and Non-Linear Models”. The nomination of professorship took place in 2003. The research field of the professorship is hydraulics in mobile machines.
His main research interests are autonomous mobile machines. He has supervised 9 doctoral theses and about 100 master theses. He has over 100 scientific publications and four patents. He has been member of scientific program committees of conferences in Aachen, Dresden, Linz, Hangzhou, Linköping and Tampere.
Abstract: Laboratory of Automation and hydraulic engineering (AUT) in Tampere University of Technology (TUT) has been studied remote or autonomous off-road vehicles since 2000. This paper will give the state-of-art of the previously introduced research group work results.
Future worksites will be occupied by different level of automation work machines. How these machines are working individually and how a fleet of these machines cooperates is discussed. The sliding autonomy machines is described and defined in the paper. The automation levels are no automation, operator assistance system and autonomous one. These different cases is handled via examples. The studied off-road vehicle is a wheel loader. It can be controlled manually, remote operated or autonomously.
The required control strategies, sensors, and algorithms for operating with autonomous wheel loader are studied and presented in the paper. The control strategy is consisting of e.g. static and dynamic mapping, path planning, obstacle observation and avoidance. In the autonomous machines and also in machines where operator assistance system is active the situational awareness is the key research field. How we are sensing the surroundings of the machine with the today’s sensors is presented in the paper.
Power management and energy efficiency in hydraulic work machines are still active fields of research. Multiple architectures and configurations have been suggested concerning this field. In addition, implemented solutions that consider an entire machine are rarely presented. This paper introduces the research work of the control systems which are minimizing the fuel consumption. Compared to traditional controls, the new methods both reduce the fuel consumption and extend the operating range of a machine.
Special Lecture 2 (FIT Hall) : Oct. 27 (Fri.), 2017
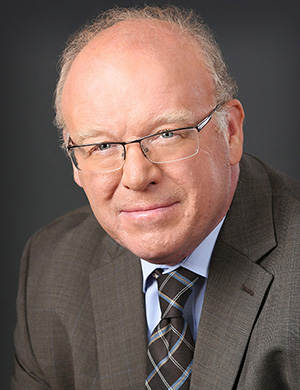
"Energy Saving Technology for Commercial Off-highway Vehicles"
Prof. Kim STELSON, U.S.A.
College of Engineering Distinguished Professor and Director,
NSF Engineering Research Center for Compact and Efficient Fluid Power
Department of Mechanical Engineering
University of Minnesota
Minneapolis, MN 55455 U.S.A.
Kim A. Stelson is Director of the NSF-funded Engineering Research Center for Compact and Efficient Fluid Power. He is College of Science and Engineering Distinguished Professor in the Department of Mechanical Engineering at the University of Minnesota where he has been since 1981. He received his B.S. degree in mechanical engineering from Stanford University in 1974 and his S.M. and Sc.D. degrees in mechanical engineering from M.I.T. in 1977 and 1982. Stelson's fluid power research includes work on hydraulic hybrid vehicles and hydrostatic transmissions for wind power. He has been a visiting faculty member at Hong Kong University of Science and Technology, the University of Auckland and the University of Bath. He has previously been Director of the Design and Manufacturing Division and Director of Graduate Studies for the M.S. in Manufacturing Systems Program at the University of Minnesota. Stelson has been an Associate Technical Editor of the Journal of Dynamic Systems, Measurement and Control, a journal that has twice awarded him the Rudolf Kalman Best Paper Award. He is a Fellow of the American Association for the Advancement of Science and has been awarded the ASME Robert E. Koski Award for contributions to fluid power.
Abstract: Commercial off-highway vehicles for construction, agriculture, mining and forestry rely on fluid power for propulsion, steering and work circuits. These systems consume 0.4-1.3 x 1018 joules per year in the United State with a remarkably low average fluid power transmission efficiency of 21%. The large amount of energy and low efficiency of transmission means that fuel use and CO2 emissions could be greatly reduced by improving the fluid power technology in commercial off-highway vehicles. Recognizing this need, the United States Congress appropriated $5 million in 2017 for the creation of a university-industry collaborative research program for improving the efficiency of commercial off-highway vehicles. The campaign to educate and encourage government action in this neglected area was led by the Center for Compact and Efficient Fluid Power (CCEFP). CCEFP will continue to nurture this program in the future with the ultimate goal of continuous funding of $10 million per year. In this talk the structure and approach of this program will be described. Examples will be given of several pre-competitive energy saving projects being developed in the United States.
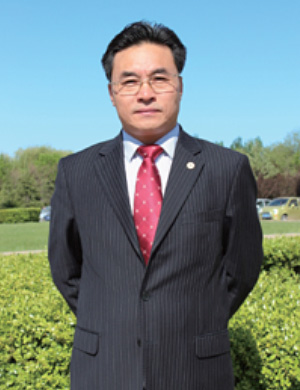
"Hydraulic Wind Turbine"
Prof. Xiangdong KONG, China
Yanshan University
Xiangdong Kong received the B.S. degree from Zhejiang University in 1982, and received Ph.D. Degree from Northeast Heavy Machinery Institute in 1991. He has been a Professor since 1997. He currently serves as chairman of the Fluid Power Transmission and Control Institution CMES, the director of the Key Laboratory of Fluid Power Transmission and Control of Heavy Machinery in Hebei Province and the director of the Mechanical Engineering Society of Hebei Province. His research interests include electro hydraulic servo control system, heavy machinery fluid transmission and control, etc.
Abstract: The lecture is divided into two parts. In the first part, mainly introduce the current situation of the Fluid Power Transmission and Control Institution CMES, including the development situation, the academic exchange activities etc. In the second part, focuses on the research of the Hydraulic Wind Turbine (HWT). The HWT is a new type of wind turbine which uses quantitative pump-variable displacement motor hydraulic transmission system, can reduce wind turbine nacelle weight and reduce the cost. In order to meet the requirements of grid and improve the power quality, it is necessary to solve the problems of hydraulic system speed control, system power control, long pipeline resonance suppression control and low voltage ride through etc. To validate the performance of HWT, a 60KVA hydraulic wind turbine experimental platform has built at Yanshan University.
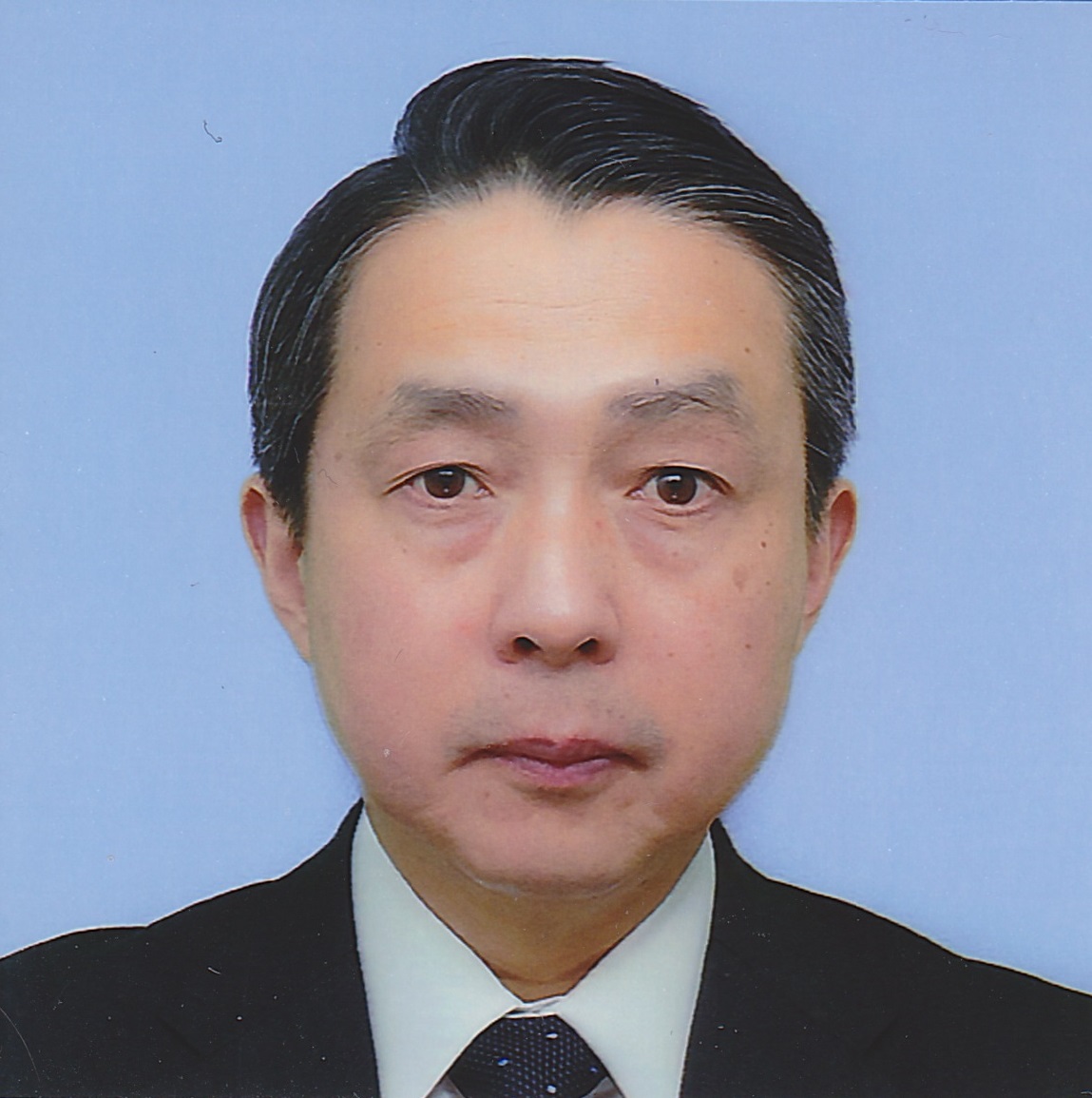
"The 10th Anniversary Symposium for the Future of Fluid Power"
Prof. Kazushi SANADA, Japan
Kazushi SANADA received the B.S., M.S., and Dr. degrees in control engineering from Tokyo Institute of Technology, Japan, in 1984, 1986, and 1996, respectively. He had worked for Tokyo Institute of Technology as a research assistant from 1986 to 1998. He had been an Associate Professor in Yokohama National University from 1998 to 2004. Since 2004, he has been a professor in Faculty of Engineering, Yokohama National University. His research field is modelling and control of fluid power systems including oil-hydraulics and water hydraulics. He is a vice president of the Japan Fluid Power System Society and a chairperson of the 10th JFPS International Symposium on Fluid Power FUKUOKA 2017.
Abstract: The Japan Fluid Power System Society has organized the JFPS International Symposiums on Fluid Power. The first symposium was held at Tokyo Institute of Technology, March 13-16, 1989. Since then, every three or four years, the JFPS International Symposiums on Fluid Power have been held in attractive venues, Tokyo (Sophia Univ.) 1993, Yokohama 1996, Tokyo (Tokyo Fashion Town) 1999, Nara 2002, Tsukuba 2005, Toyama 2008, Okinawa 2011, and Matsue 2014. This symposium is the 10th anniversary symposium in Fukuoka 2017. In my short presentation, the history and the future of the JFPS international symposium will be briefly introduced.